
Innovation durch Zusammenarbeit
Unsere aktuellen Forschungsprojekte
Wir sind stets offen für die Teilnahme an extern geförderten Forschungsprojekten und kooperieren mit führenden Universitäten, renommierten Forschungseinrichtungen (z.B. Fraunhofer-Institute) und innovativen Industriepartnern.
Im Fokus der Projekte stehen Zukunftstechnologien mit hohem Forschungsbedarf, die eine interdisziplinäre Zusammenarbeit erfordern. Kein Partner kann diese Herausforderungen alleine bewältigen – gemeinsame Entwicklung und Innovation stehen im Mittelpunkt.
Erfahren Sie, an welchen innovativen Lösungen wir derzeit arbeiten und welche Technologien die Zukunft gestalten werden.
Unsere Forschungsprojekte
Das Horizon Europe Forschungsprojekt BatWoMan zielt darauf ab, den Weg für eine nachhaltige und kosteneffiziente Produktion von Lithium-Ionen Batteriezellen in der Europäischen Union zu ebnen. Dies soll durch die Entfernung flüchtiger organischer Verbindungen während der Elektrodenverarbeitung und durch die Verwendung von Slurries mit hohem Trockensubstanzgehalt erreicht werden. Ein innovatives Konzept zur Reduzierung des Trockenraumbedarfs mit verbesserter Elektrolytbefüllung wird ebenso etabliert wie eine kostengünstige und energieeffiziente Zellkonditionierung, d.h. Benetzung, Formation und Alterung. Eine KI-basierte Plattform und ein digitaler Batteriedatenraum und -pass werden diese technologischen Verbesserungen unterstützen. Das Gesamtziel des Projekts ist es, die Produktionskosten und den Energieverbrauch um mehr als die Hälfte zu senken und so die Herstellung von Batteriezellen mit niedrigen Emissionen voranzutreiben.
Unser Beitrag
Im Rahmen des Projekts wird Matthews Engineering einen Kalander entwickeln, mit dem das Elektrodenmaterial in einem Schritt verdichtet und getrocknet werden kann. Verschiedene Trocknungsmethoden werden evaluiert. Der entwickelte Kalander wird dann an verschiedenen Standorten eingesetzt, um den Gesamtprozess zu testen.
Projektlaufzeit
01.09.2022 – 31.08.2025
Projektpartner
- Austrian Institute of Technology
- Karlsruhe Institut für Technologie
- Universität Duisburg-Essen
- CIDETEC
- Sovema Gruppe
- Schwedisches Forschungsinstitut
- CERTH Zentrum für Forschung und Technologie Hellas
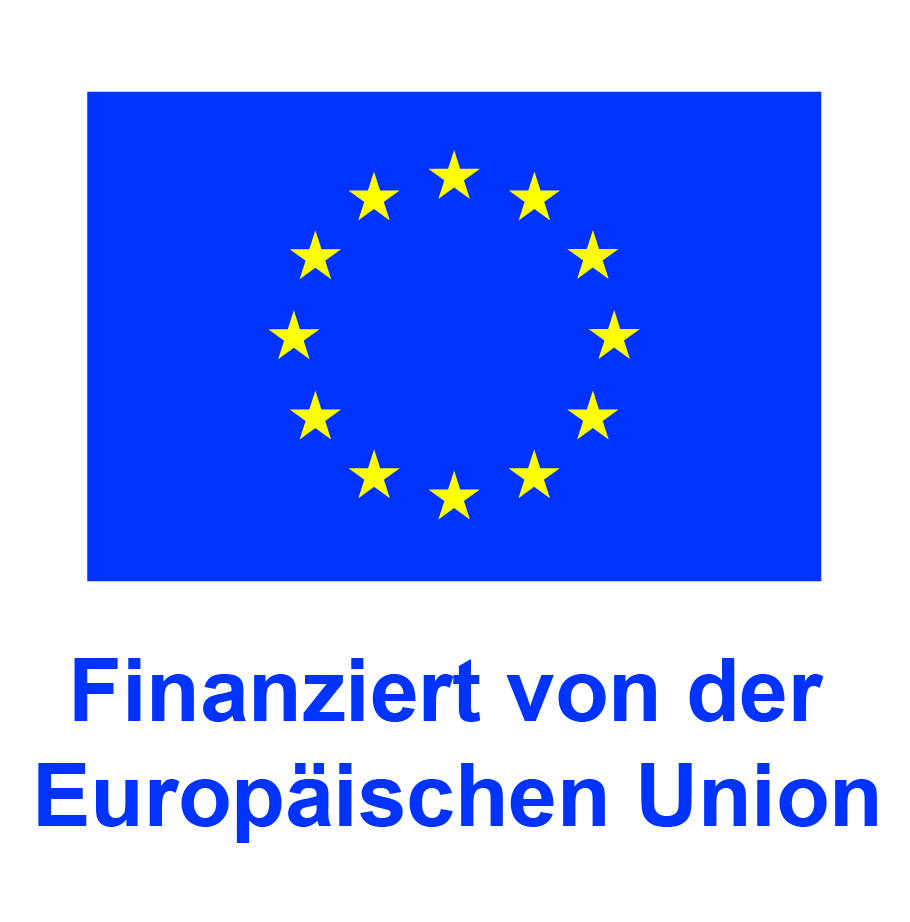
Ziel des Projektes GUTBatt ist die Entwicklung einer variablen und skalierbaren Prozesskette zur lösemittelfreien Trockenbeschichtung von Elektroden aus innovativen Materialien für Lithium-Ionen- und Lithium-Polymer-Festelektrolyt-Batteriezellen, für die auch ein Konzept für eine vernetzte Pilotanlage entwickelt werden soll. Im Rahmen des Projektes werden zunächst mögliche lösemittelfreie Prozessrouten und Sicherheitskonzepte untersucht und anschließend ein Trockenbeschichtungsverfahren für Flüssig-Elektrolyt-Batterien im Labormaßstab etabliert. Darauf aufbauend werden die etablierten Prozesse in den Pilotmaßstab hochskaliert, um eine kontinuierliche Produktion von mehreren Metern pro Minute zu ermöglichen. Da auch polymerbasierte Festkörperbatterien zunehmend an Interesse gewinnen, wird anschließend auch die Anwendung der etablierten Prozessroute für polymere SSBs getestet.
Unser Beitrag
Im Rahmen des Projektes wird Matthews Engineering einen Dreiwalzenkalander entwickeln, der für die Entwicklung der Prozesskette eingesetzt wird. Außerdem wird eine Glovebox für den Kalander entwickelt, die eine flexible Verarbeitung in trockener Atmosphäre ermöglicht. Matthews unterstützt auch die Skalierung des Prozesses auf die iPAT-Pilotanlage.
Projektlaufzeit
01.06.2023 – 31.05.2026
Projektpartner
- Custom Cells Itzehoe GmbH
- TU Braunschweig
- Zeppelin Systeme GmbH
- SSL Energie
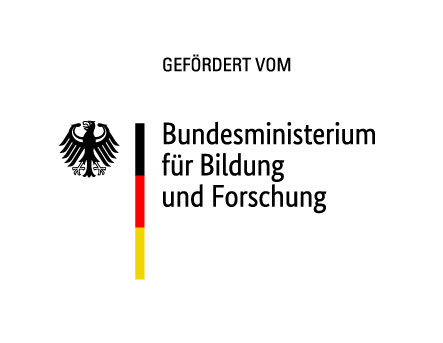
Ziel des Projektes TROMBIBATT ist die Entwicklung eines kostengünstigen und energieeffizienten Verfahrens zur Herstellung von Elektroden für Lithium-Ionen-Batterien. Bisher werden Elektroden in einem lösungsmittelbasierten Verfahren hergestellt, das aufwendige Trocknungs- und Verdichtungsschritte erfordert. Ein lösungsmittelfreies Verfahren könnte Kosten und Energieverbrauch senken, stößt aber auf Probleme bei der Homogenität der Beschichtung. Die trockenen Pulvermischungen sind ungleichmäßig verteilt, was die Qualität und Reproduzierbarkeit der Elektroden beeinträchtigt. Das Projekt zielt darauf ab, dieses Problem durch den Einsatz spezieller Bindemittel und Graphite zu verbessern, die eine bessere Plastifizierung und Schmierung gewährleisten. Dies bedeutet, dass keine neuen Materialkomponenten benötigt werden. Darüber hinaus wird ein kontinuierliches Extrusionsverfahren mit einem Doppelschneckenextruder entwickelt, um die Mischungsqualität zu optimieren. Die mechanische Beanspruchung der Partikel kann gezielt gesteuert werden. Anschließend werden die Pulver verdichtet und in einem Kalander zu Elektroden geformt. Die gezielte Homogenisierung des Pulvers führt zu einer besseren Verarbeitung der Werkstoffsysteme im Walzenspalt. Dies erhöht die Qualität der Elektroden und die Flexibilität des Prozesses und ermöglicht die industrielle Anwendung des Trockenbeschichtungsverfahrens.
Unser Beitrag
Compoundierte Pulvermischungen aus dem Extruder werden zu trocken hergestellten Elektroden geformt. Je nach Materialzusammensetzung (hauptsächlich Bindemittel) werden freistehende Elektroden oder ein auf der Kalanderwalze haftender Elektrodenfilm hergestellt. Saueressig übernimmt die Entwicklung von Gerätelösungen für die Abnahme von der Walze und eine Kantenkontrolle der Elektroden bei der Trockenkompaktierung. Die entwickelten apparativen Lösungen werden in die Entwicklung eines 4-Walzen-Kalanders integriert, der dann mit dem Extruder und der entwickelten Online-Sensorik zu einem kontinuierlichen Prozess kombiniert und erprobt wird.
Projektlaufzeit
01.11.2023 – 31.10.2026
Projektpartner
- Thermo Electron GmbH
- Institut für Mechanische Verfahrenstechnik und Mechanik, Karlsruher Institut für Technologie (KIT)
- Institut für Angewandte Materialien – Energy Storage Solutions, Karlsruher Institut für Technologie
- LUM GmbH
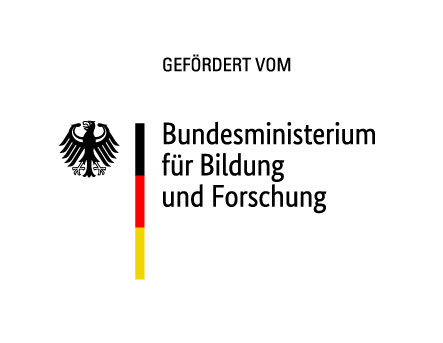
Das Projekts Grabadv verfolgt die Weiterentwicklung der Technologie zur Herstellung graphitbasierter Bipolarplatten, um deren Leistungsfähigkeit und Wirtschaftlichkeit zu optimieren.
Brennstoffzellen sind zentrale Bausteine für klimaneutrale Mobilitätskonzepte, stoßen jedoch auf technische und wirtschaftliche Hürden. Insbesondere die Qualität und die Herstellungskosten der Bipolarplatten haben einen großen Einfluss auf die Leistungsfähigkeit und Wirtschaftlichkeit. Während metallbasierte Platten leicht und dünn sind, haben sie technische Einschränkungen und benötigen oft Korrosionsschutz. Graphitverbundwerkstoffe hingegen bieten Formfreiheit, Korrosionsbeständigkeit und hohe Langzeitstabilität, ihre Leistungsfähigkeit hängt jedoch stark von Materialzusammensetzung und Verarbeitung ab.
In einem Vorgängerprojekt wurde in Zusammenarbeit mit Bosch bereits die Machbarkeit von graphitbasierten Bipolarplatten im Hochdurchsatzverfahren demonstriert. Im aktuellen Projekt sollen funktionsfähige Platten hergestellt, in Kurzstapeln getestet und die Prozesskette um Vereinzelungs- und Stanzprozesse erweitert werden.
Unser Beitrag
Im Rahmen des Projektes werden wir unsere Expertise nutzen, um die im Vorgängerprojekt etablierten Einzelprozesse weiterzuentwickeln, zu einem Gesamtkonzept zusammenzuführen und um weitere Prozessschritte zu ergänzen.
Projektlaufzeit
01.07.2024-31.06.2027
Projektpartner
- Robert Bosch GmbH
- Universität Stuttgart, Institut für Kunststofftechnik
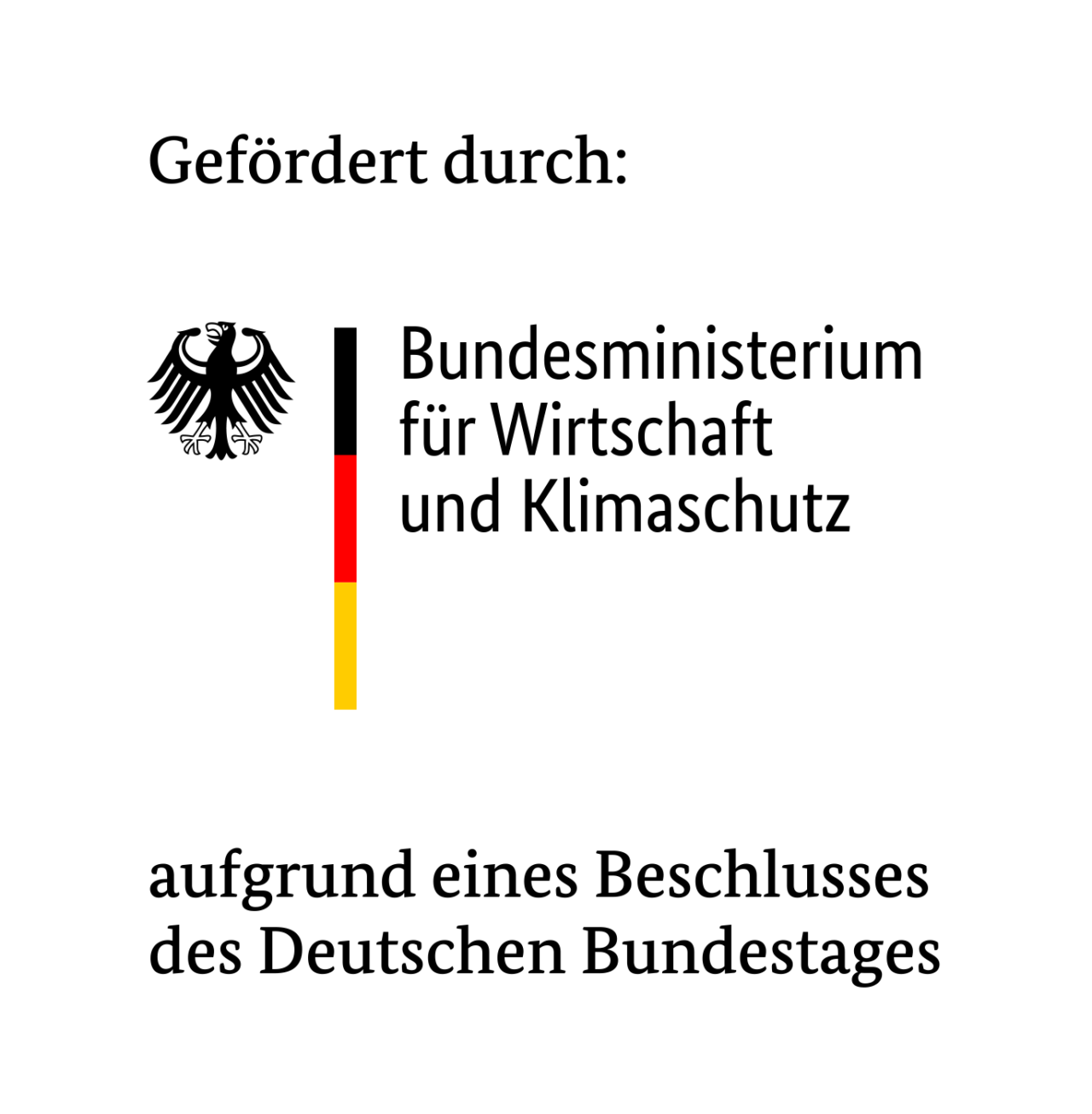
Im Zuge des technologischen Wandels, der durch den Klimawandel vorangetrieben wird, rücken Lithium-Ionen-Batterien als Schlüsselkomponenten zur Energiespeicherung und -bereitstellung immer mehr in den Fokus. Die kontinuierliche Erforschung von Technologien zur Erhöhung der Energiedichte und Leistungsfähigkeit dieser Batterien hat zu einer Reihe von Innovationen geführt. Unter diesen innovativen Ansätzen nimmt das Verfahren der Walzenstrukturierung eine vielversprechende Position ein. Durch die gezielte Modifikation der Elektrodenstruktur verspricht diese Technologie nicht nur eine verbesserte Leistungsfähigkeit, sondern ermöglicht auch größere Schichtdicken und eröffnet damit das Potenzial für eine kostengünstigere Massenproduktion von Lithium-Ionen-Batterien.
Ziel des Projektes HoWaLIB ist das Upscaling der Walzstrukturierung von Elektroden für Lithium-Ionen-Batterien. Dazu wird ein Anlagenkonzept für den Hochdurchsatzbetrieb entwickelt und validiert. Dies beinhaltet auch die Entwicklung geeigneter Reinigungs- und Instandhaltungsstrategien. Darüber hinaus wird das Degradations- und Verschmutzungsverhalten von strukturierten Walzen untersucht und Wissen zur Herstellung geeigneter strukturierter Walzen aufgebaut. Die entwickelten Konzepte sollen in die Konstruktion eines industriellen Strukturierungskalanders überführt und gemeinsam als Innovationsmodul in das FFB integriert werden.
Unser Beitrag
Unser Teilprojekt umfasst die Entwicklung und Validierung eines voll funktionsfähigen Strukturierungskalanders für die simultane Strukturierung und Kalandrierung von beschichtetem Elektrodenmaterial, die Inline-Erkennung von Walzenverschleiß und -verschmutzung sowie die Entwicklung und Erprobung von Gegenmaßnahmen. Darüber hinaus wird ein Konzept zur kostengünstigen Herstellung der benötigten strukturierten Walzen entwickelt und erprobt.
Projektlaufzeit
01.01.2025-31.12.2027
Projektpartner
- Fraunhofer FFB
- TU München
- MANUGY GmbH
Presseartikel
SAUERESSIG Group – Walzstrukturierung in der Elektrodenproduktion – HoWaLIB
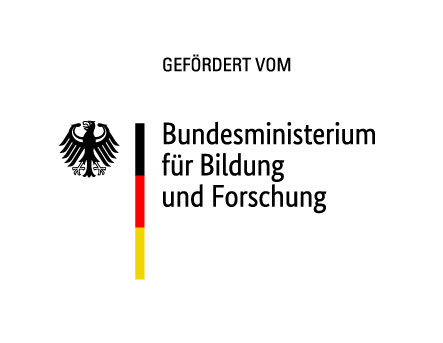
Elektroden, die das Herzstück einer Li-Ionen-Batteriezelle bilden, werden derzeit in einem Nassfilmprozess hergestellt, bei dem eine Suspension über eine Schlitzdüse auf eine Stromkollektorfolie aufgetragen und anschließend getrocknet wird, wobei das Lösungsmittel entfernt wird. Das Fraunhofer IKTS hat ein Verfahren entwickelt, bei dem hochviskose Pasten mit hohem Feststoffanteil (Reduzierung des Lösungsmittels auf 10-15 Gew.-%) über einen Extruder mit Schlitzdüse direkt auf einen Stromkollektor aufgetragen werden. Anschließend werden die Elektroden mit einer Schutzfolie überrollt, um die Haftung der Beschichtung auf dem Stromabnehmer zu verbessern. Abschließend werden die Elektroden in einer kurzen Trockenstrecke getrocknet.
Das übergeordnete Ziel von SkaleD ist die Skalierung dieses Direktextrusionsprozesses und die Validierung der Prozesskopplung in einer industrienahen Umgebung. Neben der Skalierung wird auch die Einführung von Innovationen in den bestehenden Prozess (d.h. die Integration eines NIR-Moduls und die Möglichkeit der simultanen beidseitigen Beschichtung) im Vergleich zum bestehenden Laborprozess hinsichtlich Effizienz (Energie, Kosten, Zeit, Raum) vorangetrieben. Mit dieser Weiterentwicklung und Skalierung des Direktextrusionsprozesses kann diese Technologie an industrielle Standards und Anforderungen herangeführt und in Richtung einer ressourcenschonenden und effizienten Batteriezellenproduktion umgesetzt werden.
Unser Beitrag
Im Rahmen des Projektes wird ein Kalander zum Laminieren und Glätten der direkt extrudierten Elektrodenschicht auf die Stromkollektorfolie entwickelt und hergestellt. Darüber hinaus werden verschiedene Ansätze für Innovationen im Walzenkonzept entwickelt und validiert. Durch die Auswahl eines geeigneten Walzenoberflächenmaterials soll die Verwendung einer Schutzfolie beim Laminieren vermieden werden (Ressourceneffizienz). Die Temperierung der Walzen bietet die Möglichkeit einer effizienteren Trocknung (Wegfall eines zusätzlichen Trocknungsschrittes). Darüber hinaus ist das Walzendesign so ausgelegt, dass eine hohe Kantenqualität mit geraden/homogenen Kanten erzeugt wird und der derzeit erforderliche nachgeschaltete Schneidprozess und der damit verbundene Abfall entfällt.
Projektlaufzeit
01.01.2025 – 31.12.2027
Projektpartner
- Fraunhofer FFB
- Fraunhofer IKTS
- EAS Batterien GmbH
- MANUGY GmbH
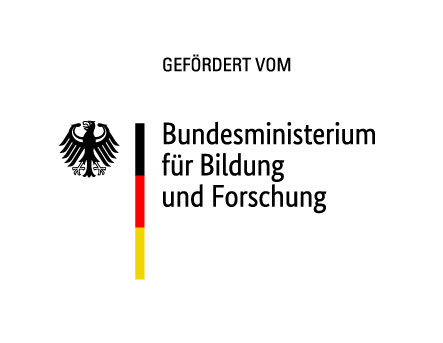
Ziel des Verbundprojektes BiPro2Scale ist es, ein innovatives Strömungsfeldkonzept für großflächige, metallische Bipolarplatten (BPP) produktionstechnisch, energieeffizient und kostengünstig umzusetzen. Diese skalierbaren BPP sollen eine bisher unerreichte Leistungsdichte von über 1 MW in einem einzigen Stack ermöglichen. Gleichzeitig soll die Lebensdauer der Stacks durch die Erforschung und den Einsatz alternativer Materialien für die metallische BPP, die Beschichtung und die Dichtung deutlich erhöht werden. Im Fokus des Vorhabens steht daher der ganzheitliche Wertschöpfungsprozess des BPP, beginnend mit dem Folienhalbzeug und dessen Umformung zu Bipolarplatten (BHP), über die Beschichtung und das Fügen der einzelnen Halbplatten bis hin zur Dichtheitsprüfung des BPP im gefügten bzw. montierten Zustand. Dabei werden sowohl die einzelnen Produktionsschritte als auch deren technische und wirtschaftliche Wechselwirkungen untereinander betrachtet.
Unser Beitrag
Matthews Engineering ist in diesem Projekt für die Entwicklung der Rotationsprägetechnologie verantwortlich. Dies beinhaltet die Entwicklung der notwendigen Anlagentechnik und der Prägewalzen. Dies geschieht im Vergleich zum statischen Prägen und in enger Abstimmung mit den nachgelagerten Prozessen. Am Ende des Projektes ist die Herstellung einer Demonstrator-Bipolarplatte mit einer Strömungsfeldfläche von 1000 cm² geplant.
Projektlaufzeit
01.01.2025 – 31.12.2027
Projektpartner
- Cellform Hydrogen GmbH & Co. KG
- VON ARDENNE GmbH
- Weil Technologie GmbH
- C-marx GmbH
- ZELTWANGER Holding GmbH
- HoKon GmbH & Co. KG
- Deutsches Zentrum für Luft- und Raumfahrt e.V. (DLR)
- Universität Stuttgart Institut für Umformtechnik (IFU)
Presseartikel
Verbundprojekt für Brennstoffzellen der Zukunft: BiPro2Scale – SAUERESSIG Group
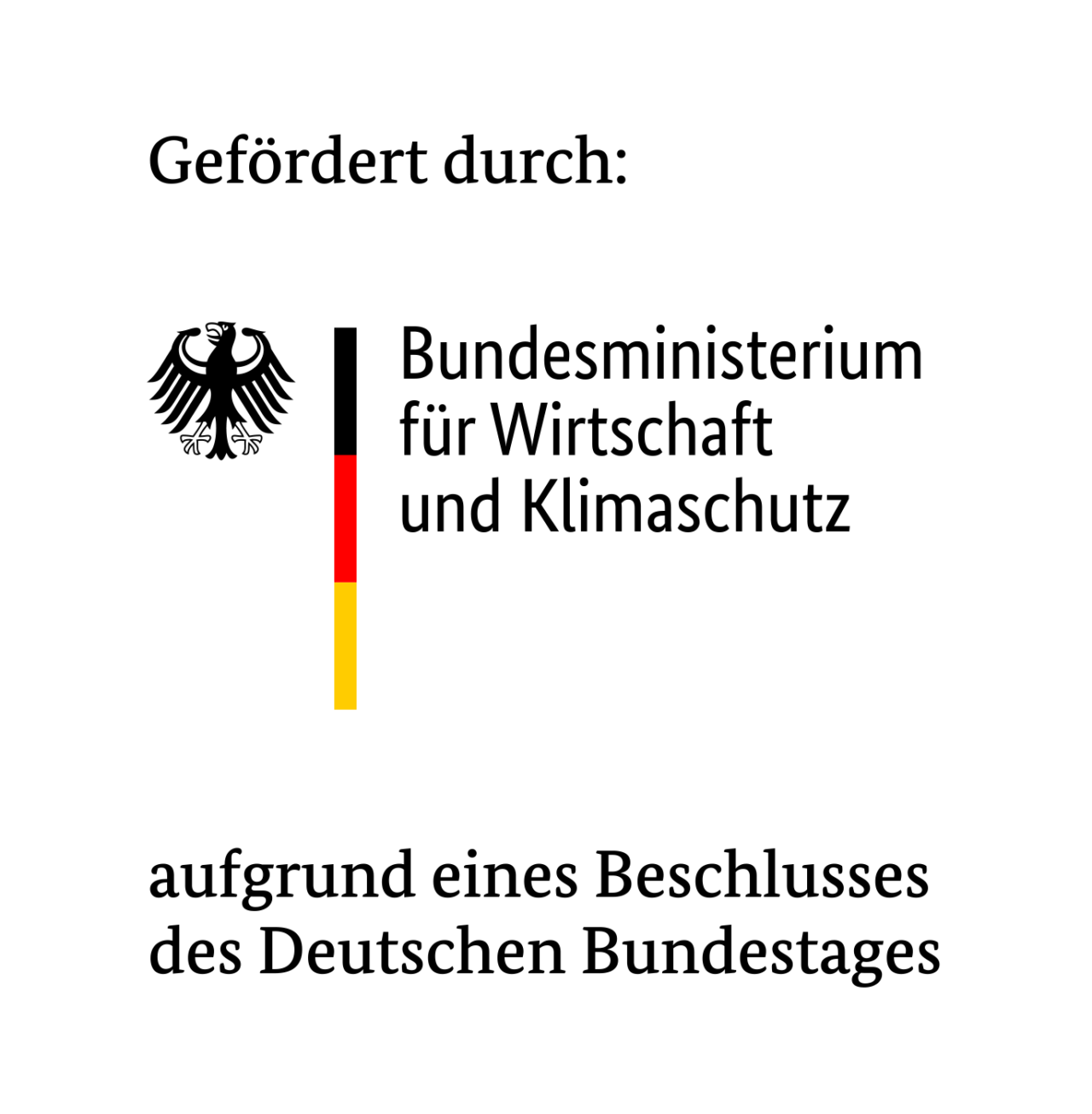
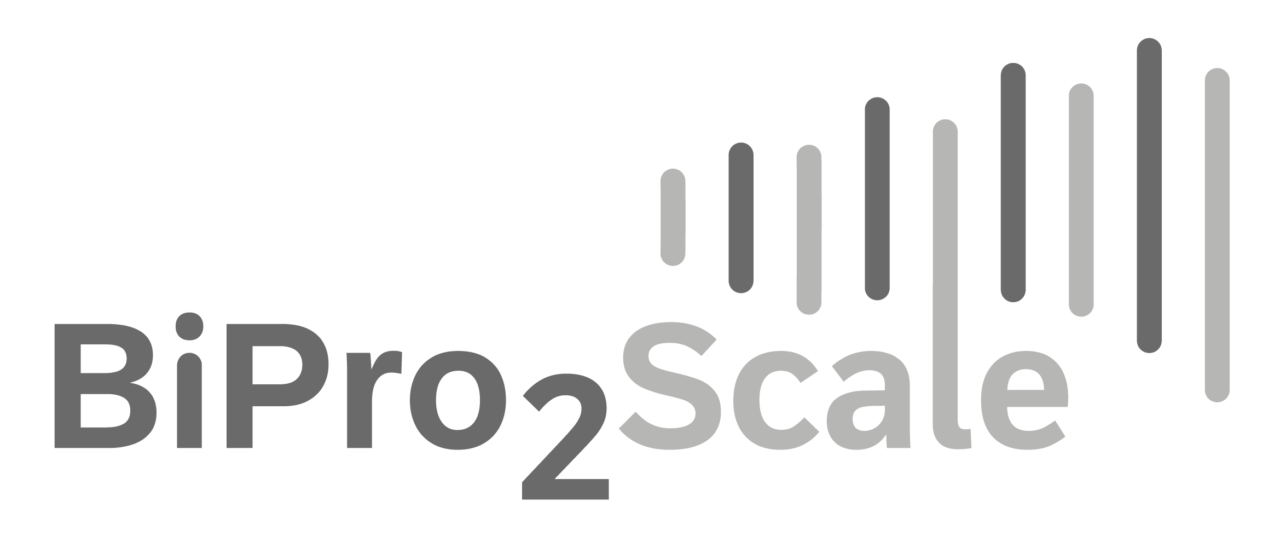