Joint project for fuel cells of the future: BiPro2Scale

Holistic product and process development of scalable bipolar plates for the implementation of innovative fuel cells for CO₂-neutral applications
The project addresses the development of PEM fuel cells for a power range of at least 1 megawatt for aviation, maritime applications and rail transportation as well as for stationary power generation systems. Achieving such power ranges with PEM fuel cells requires upscaled bipolar plates (BPPs) with an area of at least 1000 cm², necessitating a complete rethinking of both product and process development.
From a product engineering perspective, the project will develop new approaches for media supply and distribution within the bipolar plate (BPP) and the fuel cell stack, as well as for forming and joining processes, and for coating and sealing concepts required to realize such BPPs.
Nine companies and institutions are participating in the project: CellForm Hydrogen GmbH & Co. KG, Matthews International GmbH, VON ARDENNE GmbH, Weil Technology GmbH, C-marx GmbH, ZELTWANGER Holding GmbH, HoKon GmbH & Co. KG, the German Aerospace Center (DLR) and the University of Stuttgart, Institute for Metal Forming Technology (IFU).
The project is also supported by 11 associated national and international participants, including Zeppelin Power Systems GmbH, H2FLY GmbH, TRUMPF SE & Co. KG, SIEMENS, Wickeder Westfalenstahl GmbH, ZAPP Precision Metals GmbH, Raziol Zibulla & Sohn GmbH, HYDAC International GmbH, Enapter GmbH, Electric Hydrogen GmbH & Co. KG and Altair Engineering GmbH.
The project is funded by the Federal Ministry for Economic Affairs and Climate Protection as part of the funding program “Applied Non-Nuclear Research” in the 8th Energy Research Program “Innovation for the Energy Transition”.
Project objective
The BiPro2Scale joint project aims to implement an innovative production-oriented concept for large-format, highly scalable metallic bipolar plates (BPPs) in an energy-efficient and cost-effective way. In the long term, these BPPs are expected to enable a power output of over 1 MW per stack – a level not previously achieved. At the same time, alternative materials for the BPP substrate, coating, and sealing will be investigated and applied in order to significantly extend the service life of the stacks.
The project targets the entire value creation process for BPPs, beginning with the foil-based semi-finished product and its forming into bipolar half plates (BHP), the joining of these individual half plates, and finally the leak testing and coating of the BPP in the joined respectively in the assembled state. Individual manufacturing steps and their technical and economic interdependencies are examined. The flow-field design for large-scale BPPs to be developed within the project, will be continuously evaluated from both a product performance and a sustainable and economical manufacturing perspective. To achieve this overall objective, the consortium is pursuing an integrated and interdisciplinary development strategy as described below.
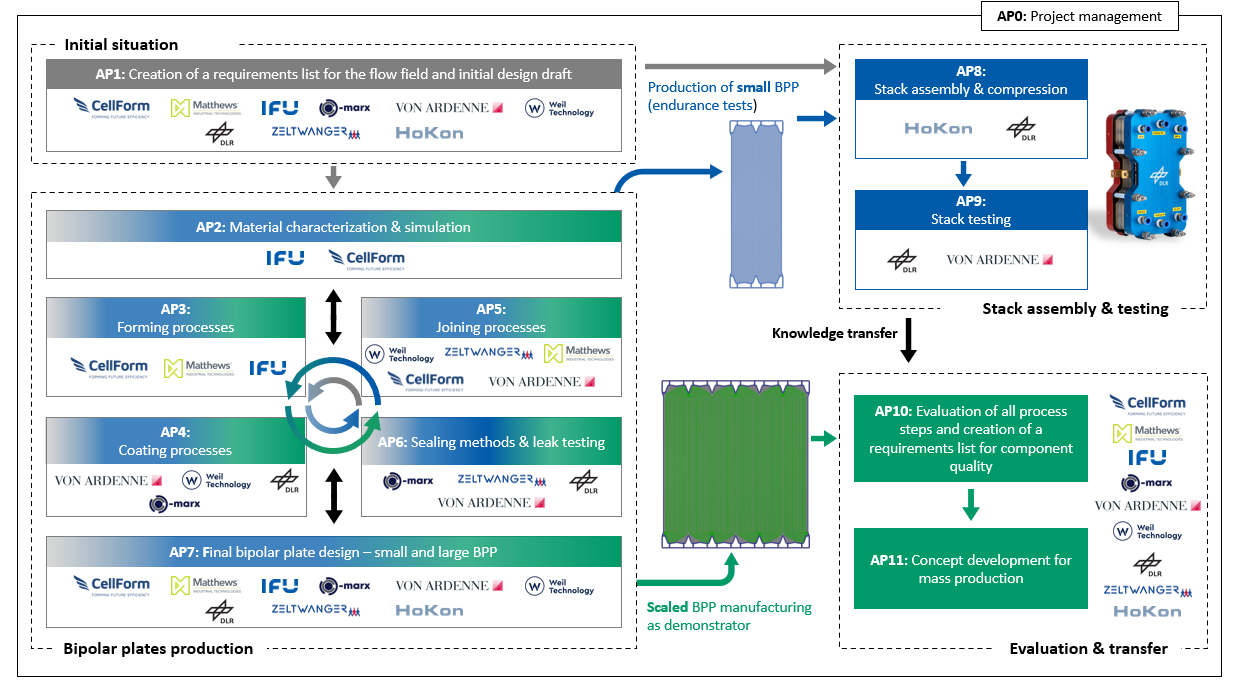
Significance and outlook
The know-how developed for the production of large-format scalable BPPs is consolidated in a virtual production concept, and the potential for industrial-scale series production is assessed. Thanks to the collaboration of the consortium, which connects renowned participants from both industry and academia, the BiPro2Scale joint project has the potential to become a pioneer for the industrial production of scaled BPPs for PEMFCs with a power output exceeding 1 MW. In terms of the EU’s total greenhouse gas emissions, this presents a savings potential of over 8% – with the trend expected to rise. All participating industrial companies consider the results as an integral part of their future strategy and plan to integrate the developed technical systems within their business areas to open up new markets.
Each project participant will act as a multiplier for the results achieved, both during the project’s duration and after its completion, thereby directly transferring innovations into the fuel cell industry. Furthermore, the academic participants in the consortium will publish parts of the results in specialist journals and present them as papers at national and international meetings and conferences, aiming to increase the visibility of the participating German institutes in research areas of fuel cell technology, both domestically and internationally.
The involvement of industrial companies and research institutions ensures a targeted balance between innovation and the feasibility of the technological and scientific project goals. This guarantees that the scientific content developed in areas such as BPP design, simulation methods, and production processes can be applied in an industrial context in a timely manner and meets the requirements and objectives of the participating industrial companies.
Learn more about our Fuel Cell Solutions.