
Innovation through collaboration
Our current research projects
We are always open to the possibility of participating in externally funded research projects and cooperate with leading universities, renowned research institutes (e.g. Fraunhofer Institutes) and innovative industrial partners.
The projects focus on future technologies with high research needs that require interdisciplinary cooperation. No single partner can meet these challenges alone – the focus is on joint development and innovation.
Find out what innovative solutions we are currently working on and what technologies will shape the future.
Our research projects
The Horizon Europe research project BatWoMan aims to pave the way for sustainable and cost-effective production of lithium-ion battery cells in the European Union. This will be achieved by removing volatile organic compounds during electrode processing and by using high dry matter slurries. An innovative concept to reduce dry space requirements with improved electrolyte filling will be established, as well as cost-effective and energy-efficient cell conditioning, i.e. wetting, formation and aging. An AI-based platform and a digital battery data room and passport will support these technological improvements. The overall goal of the project is to reduce production costs and energy consumption by more than half, thereby advancing the production of low-emission battery cells.
Our contribution
As part of the project, Matthews Engineering will develop a calender capable of compacting and drying the electrode material in a single step. Different drying methods will be evaluated. The developed calender will then be used at various sites to test the overall process.
Project Duration
01.09.2022 – 31.08.2025
Project Partner
- Austrian Institute of Technology
- Karlsruhe Institute of Technology
- University of Duisburg-Essen
- CIDETEC
- Sovema Group
- Swedish Research Institute
- CERTH Center for Research and Technology Hellas
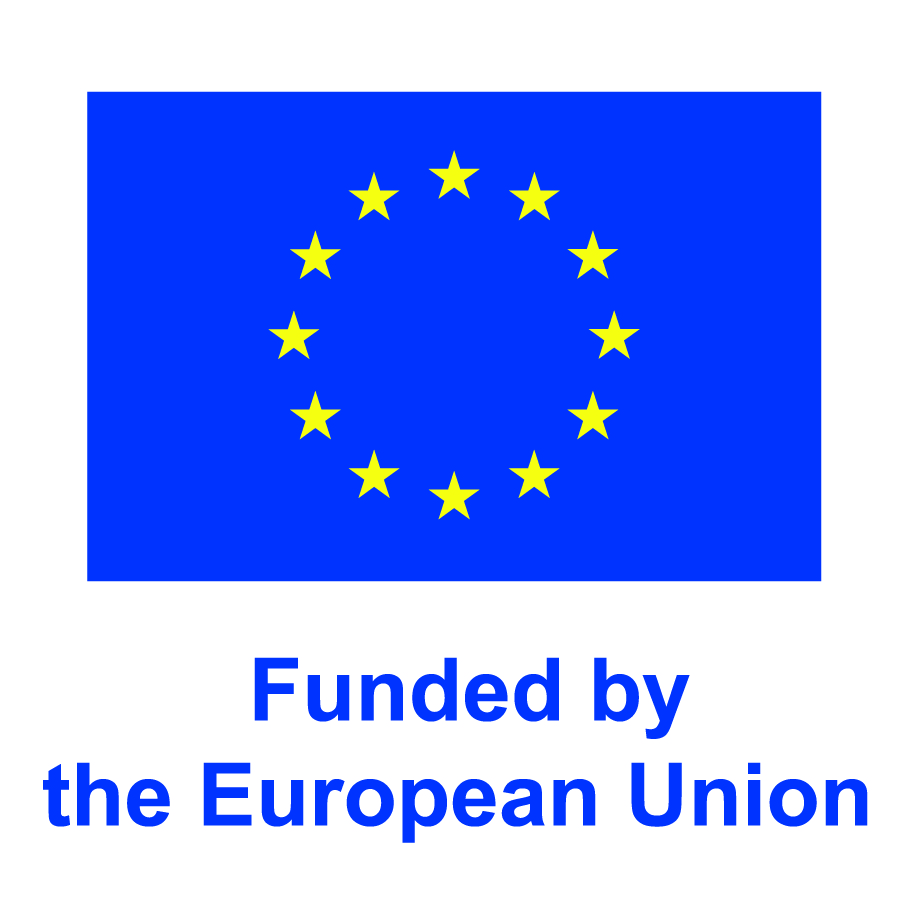
The aim of the GUTBatt project is to develop a variable and scalable process chain for the solvent-free dry coating of electrodes made of innovative materials for lithium-ion and lithium-polymer solid electrolyte battery cells. The project will first investigate possible solvent-free process routes and safety concepts, and then establish a dry coating process for liquid electrolyte batteries on a laboratory scale. Based on this, the established processes will be scaled up to pilot scale to enable continuous production of several meters per minute. As polymer-based solid-state batteries are also attracting increasing interest, the application of the established process route for polymer SSBs will also be tested.
Our contribution
As part of the project, Matthews Engineering will develop a three-roll calender that will be used to develop the process chain. In addition, a glovebox for the calender will be developed to allow flexible processing in a dry atmosphere. Matthews will also support the scale-up of the process to the iPAT pilot plant.
Project Duration
01.06.2023 – 31.05.2026
Project Partner
- Custom Cells Itzehoe GmbH
- TU Braunschweig
- Zeppelin Systeme GmbH
- SSL Energie
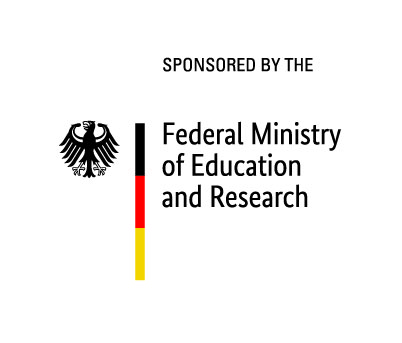
The objective of the TROMBIBATT project is to develop a cost-effective and energy-efficient process for the production of electrodes for lithium-ion batteries. To date, electrodes have been manufactured using a solvent-based process that requires complex drying and compacting steps. A solvent-free process could reduce costs and energy consumption, but there are problems with the homogeneity of the coating. The dry powder mixtures are unevenly distributed, which affects the quality and reproducibility of the electrodes. The project aims to improve this problem by using special binders and graphites that provide better plasticization and lubrication. This eliminates the need for new material components. In addition, a continuous extrusion process with a twin-screw extruder is being developed to optimize the mixing quality. The mechanical stress on the particles can be controlled. The powders are then compacted in a calender and formed into electrodes. The targeted homogenization of the powder leads to better processing of the material systems in the roll gap. This increases the quality of the electrodes and the flexibility of the process, enabling the dry coating process to be used on an industrial scale.
Our contribution
Compounded powder mixtures from the extruder are formed into dry-produced electrodes. Depending on the material composition (mainly binder), free-standing electrodes or an electrode film adhering to the calender roll are produced. Saueressig is responsible for the development of equipment solutions for removal from the roll and edge control of the electrodes during dry compaction. The developed equipment solutions will be integrated into the development of a 4-roll calender, which will then be combined with the extruder and the developed online sensor technology to form a continuous process and tested.
Project Duration
01.11.2023 – 31.10.2026
Project Partner
- Thermo Electron GmbH
- Institute for Mechanical Process Engineering and Mechanics, Karlsruhe Institute of Technology (KIT)
- Institute for Applied Materials – Energy Storage Solutions, Karlsruhe Institute of Technology
- LUM GmbH
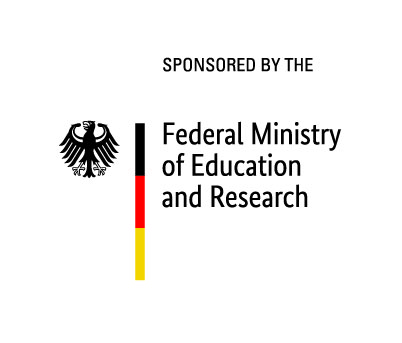
The Grabadv project will further develop the technology for manufacturing graphite-based bipolar plates to optimize their performance and cost-effectiveness.
Fuel cells are central components for climate-neutral mobility concepts, but they face technical and economic hurdles. In particular, the quality and cost of the bipolar plates have a major impact on performance and economics. While metal-based plates are lightweight and thin, they have technical limitations and often require corrosion protection. Graphite composites, on the other hand, offer freedom of shape, corrosion resistance and high long-term stability, but their performance is highly dependent on material composition and processing.
In a previous project, the feasibility of graphite-based bipolar plates in a high-throughput process was demonstrated in collaboration with Bosch. In the current project, functional plates will be produced and tested in short stacks, and the process chain will be extended to include cutting and punching processes.
Our contribution
In this project, we will use our expertise to further develop the individual processes established in the previous project, combine them into an overall concept and add further process steps.
Project Duration
01.07.2024 – 30.06.2027
Project Partner
- Robert Bosch GmbH
- University of Stuttgart, Institute for Plastics Technology
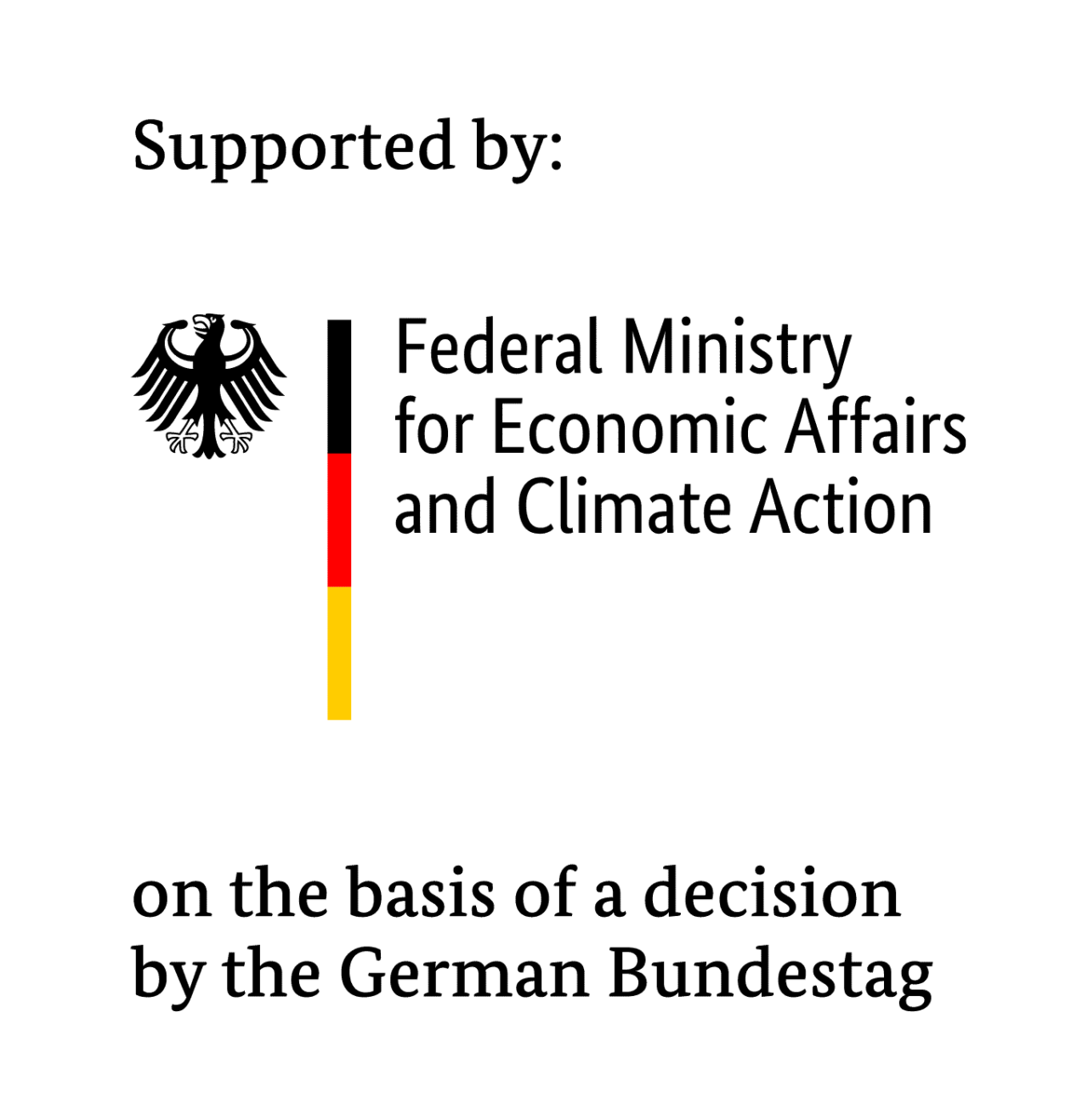
In the wake of technological change driven by climate change, lithium-ion batteries are increasingly coming into focus as key components for energy storage and delivery. Continuous research into technologies to increase the energy density and performance of these batteries has led to a number of innovations. Among these innovative approaches, roll structuring holds a promising position. By specifically modifying the electrode structure, this technology not only promises improved performance, but also allows for greater layer thicknesses, opening up the potential for more cost-effective mass production of lithium-ion batteries.
The goal of the HoWaLIB project is to upscale the roll structuring of electrodes for lithium-ion batteries. To this end, a plant concept for high-throughput operation will be developed and validated. This includes the development of suitable cleaning and maintenance strategies. In addition, the degradation and contamination behavior of structured rollers will be investigated and knowledge gained on how to produce suitable structured rollers. The developed concepts will be transferred to the design of an industrial structuring calender and integrated into the FFB as an innovation module.
Our contribution
Our subproject includes the development and validation of a fully functional structuring calender for the simultaneous structuring and calendering of coated electrode material, the inline detection of roll wear and contamination, and the development and testing of countermeasures. In addition, a concept for the cost-effective production of the required structured rolls will be developed and tested.
Project Duration
01.01.2025-31.12.2027
Project Partner
- Fraunhofer FFB
- TU Munich
- MANUGY GmbH
Press Article
SAUERESSIG Group – Roll Structuring in Electrode Production – HoWaLIB
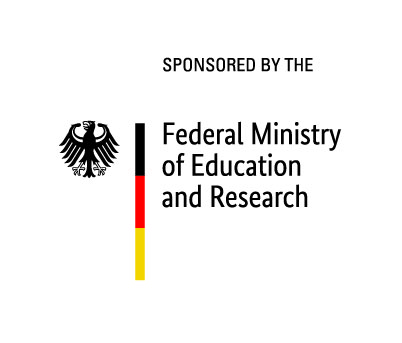
Electrodes, which form the heart of a lithium-ion battery cell, are currently manufactured using a wet film process in which a suspension is applied to a current collector foil via a slot die and then dried to remove the solvent. The Fraunhofer IKTS has developed a process in which high-viscosity pastes with a high solids content (reduction of the solvent to 10-15% by weight) are applied directly to a current collector via an extruder with a slot die. A protective film is then rolled over the electrodes to improve the adhesion of the coating to the current collector. Finally, the electrodes are dried in a short drying section.
The overall goal of SkaleD is to scale up this direct extrusion process and validate the process coupling in an industrial environment. In addition to the scale-up, the introduction of innovations in the existing process (i.e. the integration of a NIR module and the possibility of simultaneous double-sided coating) will be driven forward in terms of efficiency (energy, cost, time, space) compared to the existing laboratory process. With this further development and scaling of the direct extrusion process, this technology can be brought closer to industrial standards and requirements and implemented in the direction of resource-saving and efficient battery cell production.
Our contribution
The project will develop and manufacture a calender for laminating and smoothing the directly extruded electrode layer onto the current collector foil. In addition, different approaches for innovations in the roll concept will be developed and validated. By selecting a suitable roll surface material, the use of a protective film during lamination is to be avoided (resource efficiency). Temperature control of the rolls offers the possibility of more efficient drying (elimination of an additional drying step). In addition, the roll design is such that high quality straight/homogeneous edges are produced, eliminating the currently required downstream cutting process and associated waste.
Project Duration
01.01.2025-31.12.2027
Project Partner
- Project partners
- Fraunhofer FFB
- Fraunhofer IKTS
- EAS Batterien GmbH
- MANUGY GmbH
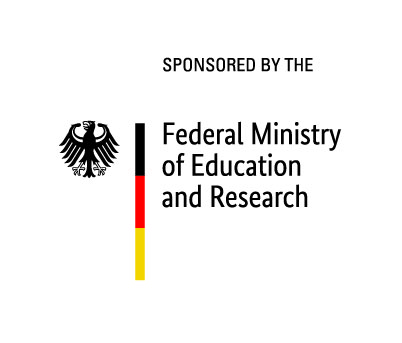
The goal of the BiPro2Scale project is to implement an innovative flow field concept for large-area metallic bipolar plates (BPP) in a production-friendly, energy-efficient and cost-effective manner. These scalable BPPs will enable an unprecedented power density of more than 1 MW in a single stack. At the same time, the stack lifetime will be significantly increased by exploring and using alternative materials for the metallic BPP, coating and sealing. The project therefore focuses on the entire value-added process of the BPP, starting with the semi-finished foil product and its forming into bipolar plates (BHP), through the coating and joining of the individual half plates, and finally to the leak test of the BPP in the joined or assembled state. Both the individual production steps and their technical and economic interactions are considered.
Our contribution
Matthews Engineering is responsible for the development of the rotary embossing technology in this project. This includes the development of the necessary equipment and the embossing rollers. This will be done in comparison to static embossing and in close coordination with the downstream processes. At the end of the project, the production of a demonstrator bipolar plate with a flow field area of 1000 cm² is planned.
Project Duration
01.01.2025-31.12.2027
Project Partner
- Cellform Hydrogen GmbH & Co. KG
- VON ARDENNE GmbH
- Weil Technologie GmbH
- C-marx GmbH
- ZELTWANGER Holding GmbH
- HoKon GmbH & Co. KG
- German Aerospace Center (DLR)
- University of Stuttgart Institute for Metal Forming Technology (IFU)
Press Article
Joint project for fuel cells of the future: BiPro2Scale – SAUERESSIG Group
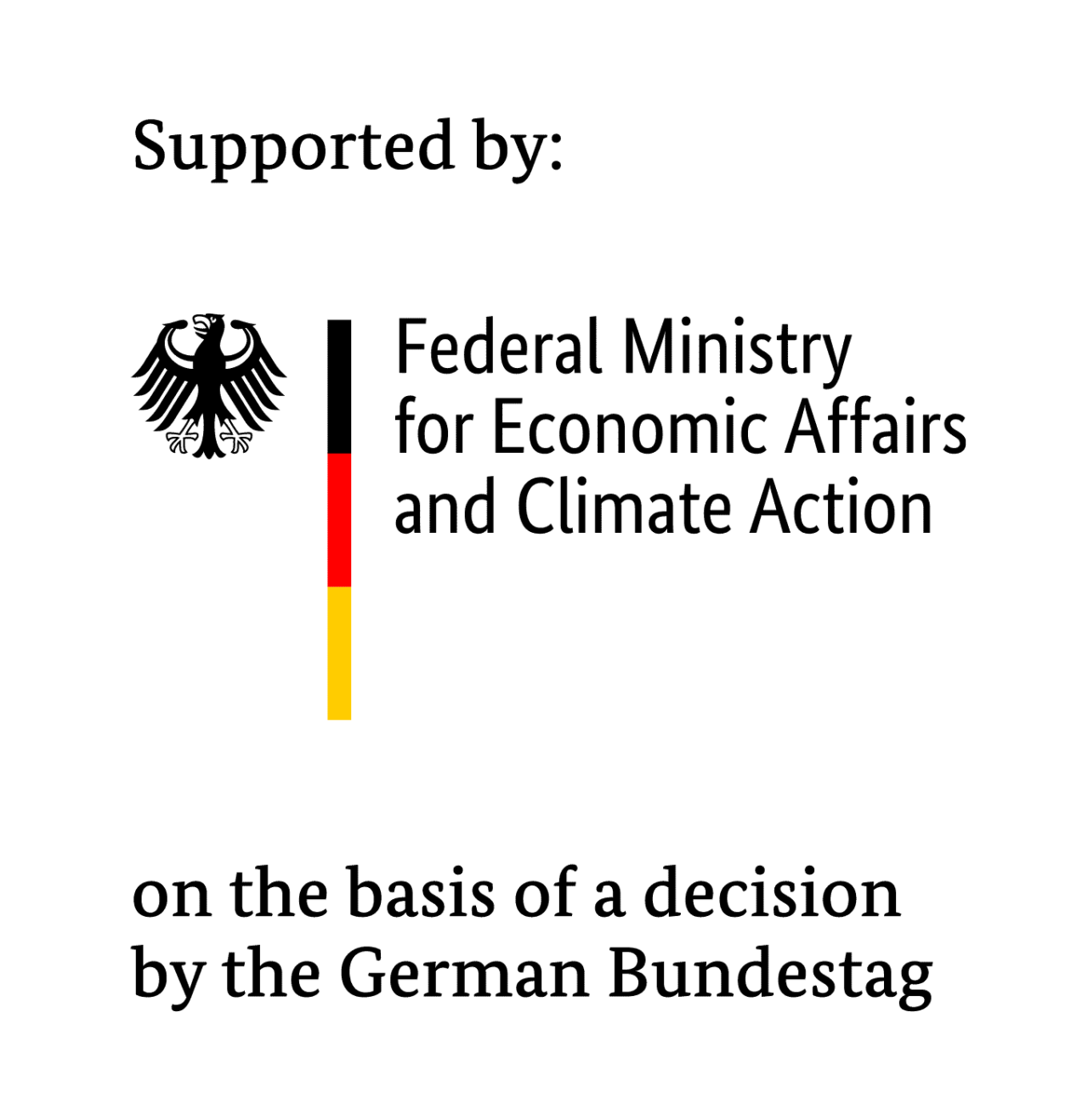
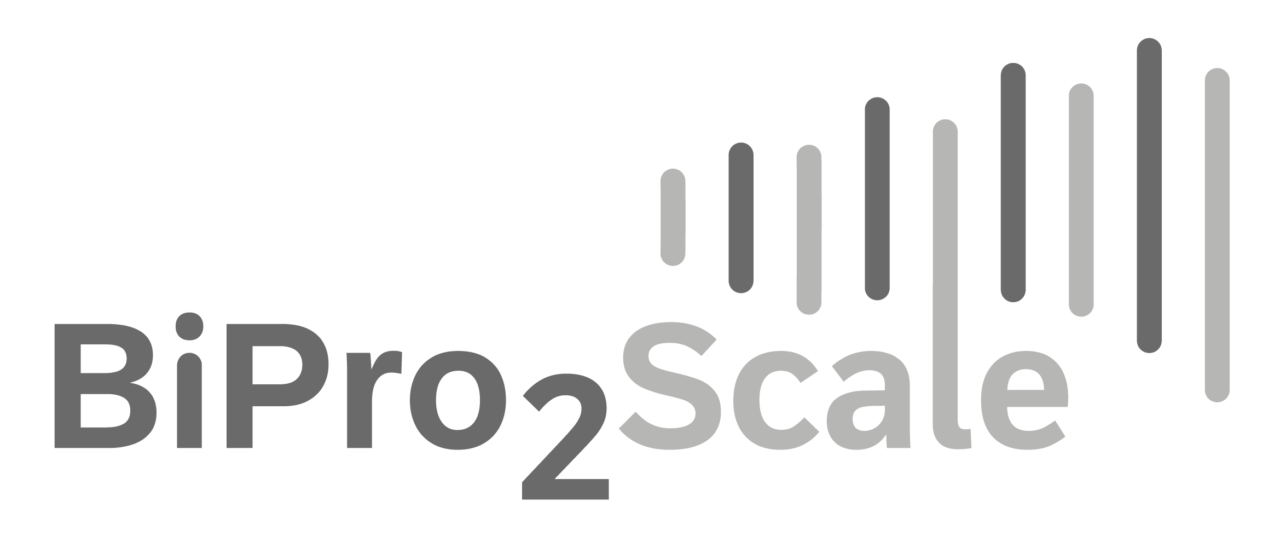